Surface Preparation and Maintenance
Thorough preparation is the key to a successful application!
Taking time now to make sure your surface is properly prepared will ensure the best possible outcome.
Apply only to concrete surfaces that are sound and solid, free of dust, dirt, grease, and oil. New concrete should be cured a minimum of 30 days. Prepare surface by mechanical means to achieve an International Concrete Repair Institute Guideline No. 03732 concrete surface profile of CSP 3.
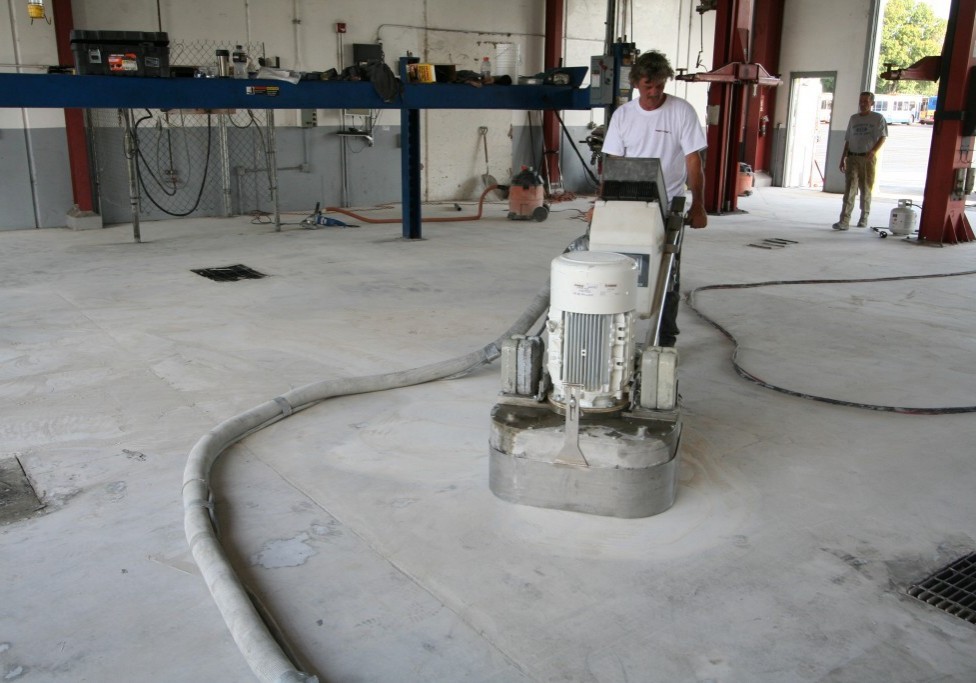
TEST FOR MOISTURE AND pH LEVELS
Moisture testing of the concrete surface should be performed. Bare concrete should be tested for pH and have a level between 7 and 11.
ASTM D-4263 - Plastic Sheet Test
Using 2” Duct tape, secure a 18”x18” sheet of transparent polyethylene to the slab, sealing it completely. Leave at least 24 hours undisturbed. Moisture under the plastic will indicate excessive moisture in the concrete and further testing in needed.
ASTM F 1869
Calcium Chloride Test, a small dish of calcium chloride is weighed and placed under a plastic cover for 24 hours. The dish is then removed and weighed again. The amount of water gained in the water vapor moisture will then determine the emission rate of the concrete. Moisture vapor transmission rate should not exceed 3 lbs. per 1000 sq.ft. in 24 hours as tested
ASTM F 2170-02
Relative humidity testing
Test the amount of moisture in the concrete by drilling a small hole in the concrete and leaving meter for 24hrs. Acceptable level less than 75%.
TEST FOR OIL AND GREASE
When oil and / or grease is present, you risk successful penetration and adherence of the High Performance Industrial Coating System. The easiest way to test for grease that is not visible is to mist water on the surface. If the water beads up, contaminants are present and must be removed. If the water is absorbed into the concrete surface, there are no oils present.
CRACK REPAIR
Proper crack repair is critical for coating appearance and performance. Use Seal-Krete Fast Cure to repair all cracks, following instructions on the label.
TEMPERATURE
Do not apply when the temperature of the concrete substrate exceeds the surrounding air temperature by more than 18° F, due to outgassing.
Outgassing - porosity in the concrete contains air. When the temperature of the concrete rises, the air in the pores expands. This may cause blisters or pin holes in the coating. An increasing surface temperature is a strong indication that outgassing will occur.
Temperature application limitations
Poly-Shell apply -20°F – 130°F
Epoxy-Shell apply 50°F – 95°F
Dura-Shell apply 50°F – 90°F
Humidity on Poly-Shell -
High humidity will reduce working time
Low humidity will increase dry time
Temperature on Epoxy-Shell -
Lower temps = slower curing times
Higher temps = fast curing times
CONCRETE PREPARATION
The surface should be roughened by mechanical means to achieve a ICRI concrete surface profile of CSP 2-3. This can be achieved by grinding or shot blasting the concrete. After preparing the surface remove all concrete dust and debris to allow good primer adhesion.
MAINTENANCE AND CARE
SEAL-KRETE High Performance Coating Systems are monolithic, making them easier to clean because dirt and contaminants remain on the surface. They are also stronger and more resistant to chemicals than many other types of flooring.
A simple mixture of a pH neutral cleaner diluted with water is recommended for regularly scheduled maintenance.
Given that debris remains on the surface, it tends to act as an abrasive and will eventually mar the finish in heavy traffic environments. Therefore, it is important that floors are properly maintained on a regular basis.
Cleaning Agents:
Do not use soap because it will create a film that is difficult to
remove with rinsing. A film left behind after cleaning causes two issues: a) the film will become slippery when wet and b) this film attracts dirt and debris which actually causes the floor to look unclean soon after it has been washed. Floor stripping agents, citrus-based cleaners and corrosive chemical degreasers are also not recommended as they can damage a floor if they are applied and let to sit for an extended period of time. A simple mixture of a pH neutral cleaner such as Simple Green® diluted with water is recommended for regularly scheduled maintenance.
Tools:
• Mops/Mop Bucket – If you have traction additives or a rougher surface such as a quartz floor, be sure to use a rayon mop instead of a cotton one. Rayon mops use synthetic fiber that is less likely to get hung up on the surface and leave fuzz balls. Use a mop bucket with a wringer and a 3-gallon standard bucket. For dust removal, use a dry mop.
• Soft-Bristled Brush – For more difficult to remove stains, a soft bristled brush may be used to agitate dirt and debris. Be sure to use a brush with soft bristles as hard bristles may mar the surface over time.
• Foam Squeegee – Use a foam squeegee after you mop to remove any excess water.
• Wet-Vacuum – For removing excess water after rinsing.
Cleaning Process:
1. Sweep entire floor to remove any loose debris and dirt with a dry mop and/or soft bristled broom. Although SEAL-KRETE HP Products cannot be penetrated, these substances will act like abrasives. If they are not regularly removed, they will wear the floor over time.
2. For everyday cleaning, use a commercially available alkaline cleaner/degreaser; follow the product’s label for more details and mixing instructions.
3. Apply a cleaning agent with a squeegee or mop and let stand for a few minutes so it can react with the surface.
4. Thoroughly mop the surface with a wet rayon mop to remove any stains. A soft bristled brush may also be used to scrub the surface.
5. Rinse the floor with clean water and use a wet vacuum or squeegee to remove. A second rinsing is also recommended to ensure that no residue is left behind. Proper attention must be paid to removing the resultant emulsion of the cleaning solution and soil.
6. Once dirty water has been removed, the floor must dry prior to returning to service.
7. Dispose of contaminated water while paying special attention to your community regulations prohibiting the introduction of certain chemicals into surface water drains and sewer systems.