Troubleshooting floor coatings
Common flooring issues when applying floor coatings.
Although thorough preparation is the key to a successful application, problems do happen, here are a few common flooring issues and how to correct and avoid them.
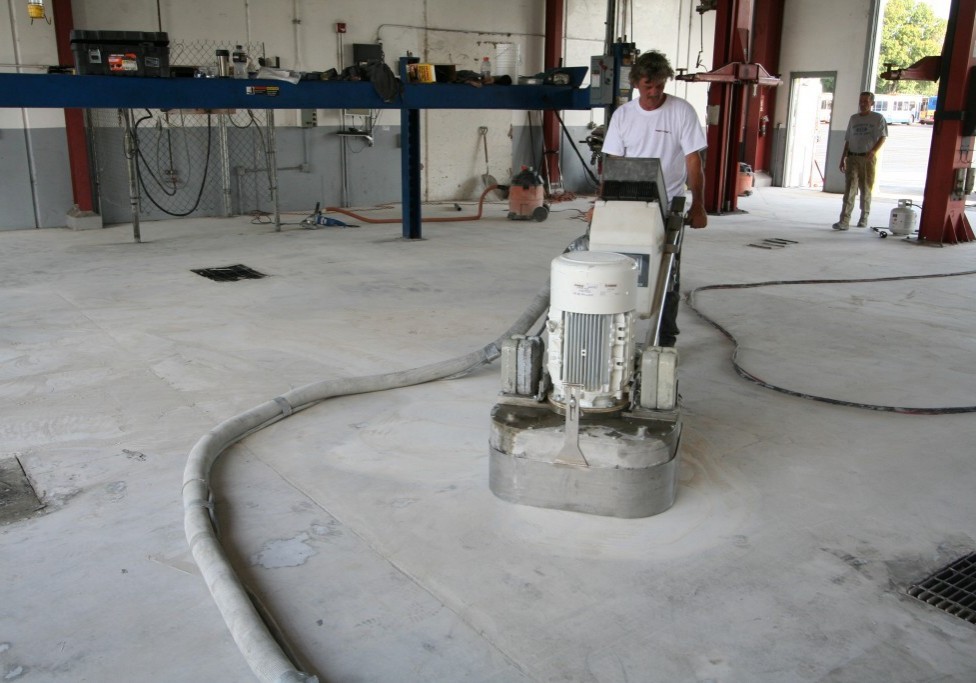
Although thorough preparation is the key to a successful application, problems do happen, here are a few common flooring issues and how to correct and avoid them.